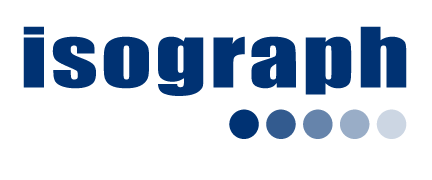
概要
必要性
故障分析の必要性
機器の信頼性を高めたい、適正な保全を実施したい場合、現在の状況を知ることが重要になります。
プラントや製品の信頼性・安全性評価
プラントや製品の信頼性や安全性評価では、実施に際して、構成要素の不信頼度や故障率情報が必要になります。 設計時に用いる不信頼度・故障率は、平均値を用います。 平均値は、ベンダー、ハンドブック、故障率ライブラリ等の値を用いることができます。
稼働中のプラントや製品についての信頼性・安全性評価(保全計画策定における問題)
ところが、保全戦略や計画の策定においては、不信頼度や故障率がどの様な特性を示すかが重要になります。 例えば、経年とともに劣化する様な機器の場合、いつ頃、不信頼度や故障率は立ち上がり始めるのかが問題となります。 また、機器は、設置環境、使用状況により同じ機種でも、壊れ方が異なります。 そこで、実際に運用中の機器や製品に対する保全戦略や計画の策定は、 設置環境、稼働状況及び重要度ごとに、故障状況や正常稼働の状況を考慮して検討する必要があります。
故障分析の有効活用
実際の故障状況や正常な稼働の状況を知る方法として、故障分析が有効です。 故障分析により、不信頼度や故障率を推定できる様になります。
サービス
故障分析及び信頼性・安全性・可用性・保全性評価支援サービスについて
弊社では、長年、培った信頼性評価システムの利用に関するノウハウを活かし、 実際の故障情報等を用いて、信頼性評価で必要となる不信頼度や故障率の分析し、 ワイブル分布や対数正規分布等を用いて数値モデル化します。 実際の故障情報から数値モデル化された不信頼度や故障率情報をデータベース化することで、 プラントや製品の可用性(稼働率)の推定やLCCの推定が可能となります。 また、RCM(信頼性中心保全)の考え方に沿って、 故障要因を排除するための取り組み(予防保全や検査など)の周期や有効性評価に繋げることが可能となります。
故障分析による故障の数値モデルと信頼性・安全性、可用性・保全性評価の関係を以下に示します。
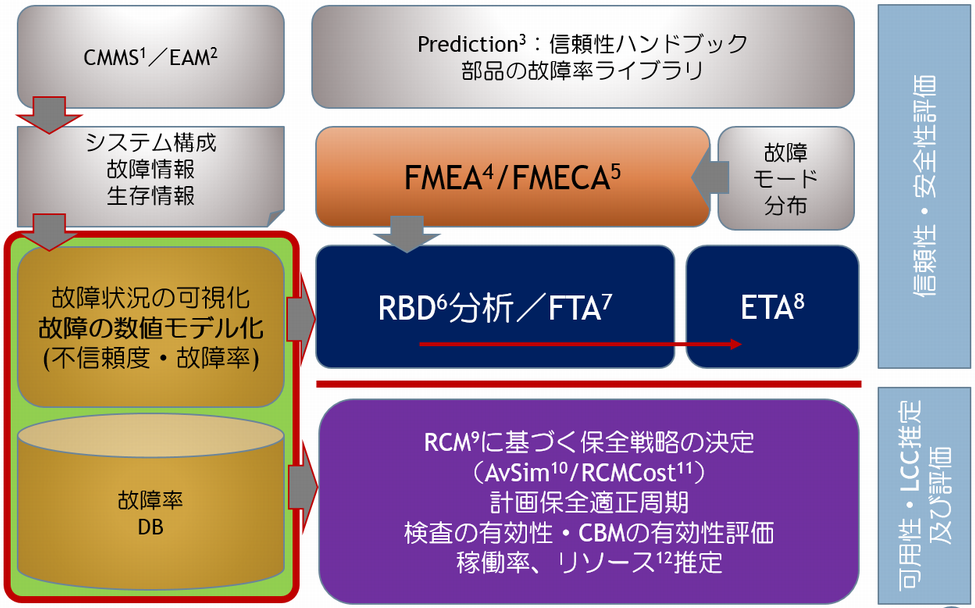
1CMMS:設備保全管理システム(Computerized Maintenance Management System)
2EAM :資産管理システム(Enterprise Asset Management)
3Prediction:信頼度予測、ハンドブック等を用いて故障率を推定
4FMEA:故障モードと影響分析
5FMECA:故障モードと影響及び致命度分析
6RBD:信頼性ブロック図分析
7FTA:フォルトツリー分析
8ETA:イベントツリー分析
9RCM:信頼性中心保全
10AvSim:Availability Workbenchの稼働率シミュレーション機能
11RCMCost:Availability WorkbenchのRCMスキームに基づく保全戦略検討支援機能
12リソース:リソースには、作業員、予備品(倉庫)、ツールの員数及び費用が存在する。
手順
サービスの概要(手順)
本サービスの概要を手順に沿って、説明します。本サービスには、以下が存在します。
- 故障情報の整理及び可視化
- 故障の数値モデル化
- 数値モデル化のまとめ
- 信頼性・安全性評価への適用支援
- 可用性(稼働率)・LCC推定及び評価への支援
故障情報の整理及び可視化
お客様よりご提示頂いた設備(機器)構成情報、故障情報を整理し可視化します。 整理では、故障の数値モデル化に先立ち機器仕様、環境、使用頻度(状況)等でグループ化した後、 故障情報の把握のために、故障発生状況を可視化します。 以下に、可視化の例を示します。
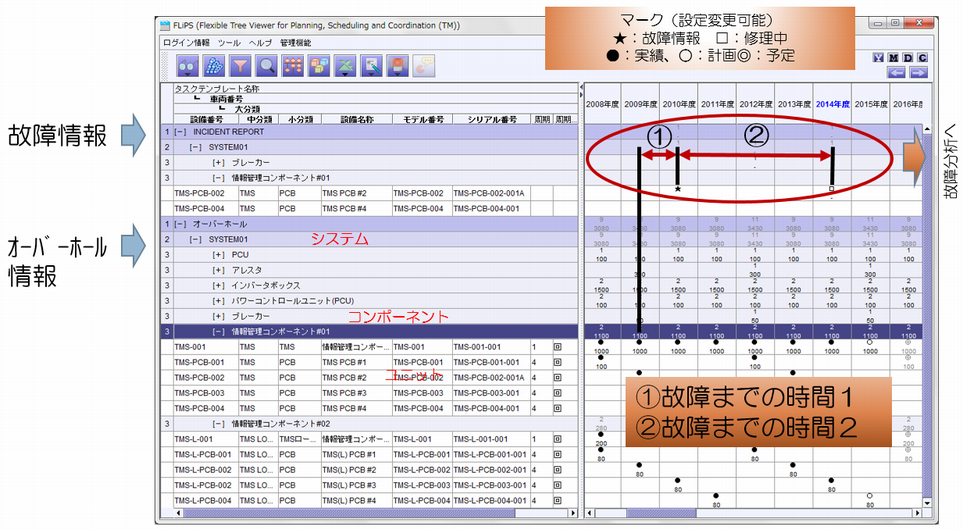
不信頼度や故障率に関する情報が少ない場合は、工夫が必要です。 実際には、保全(交換)履歴、故障していない機器の情報等を考慮することで、精度を上げます。
故障の数値モデル化
機器仕様、環境、使用頻度(状況)等にグループ化された故障情報ごとに適切な確率分布を用いて、 故障発生状況を時間に依存する数値モデルとして表します。 確率分布は、ワイブル分布、フェーズ・ワイブル分布、対数正規分布、正規分布など、お客様とご相談の上適切なものを用います。 以下に2パラメタ・ワイブル分布に近似した場合の例を示します。
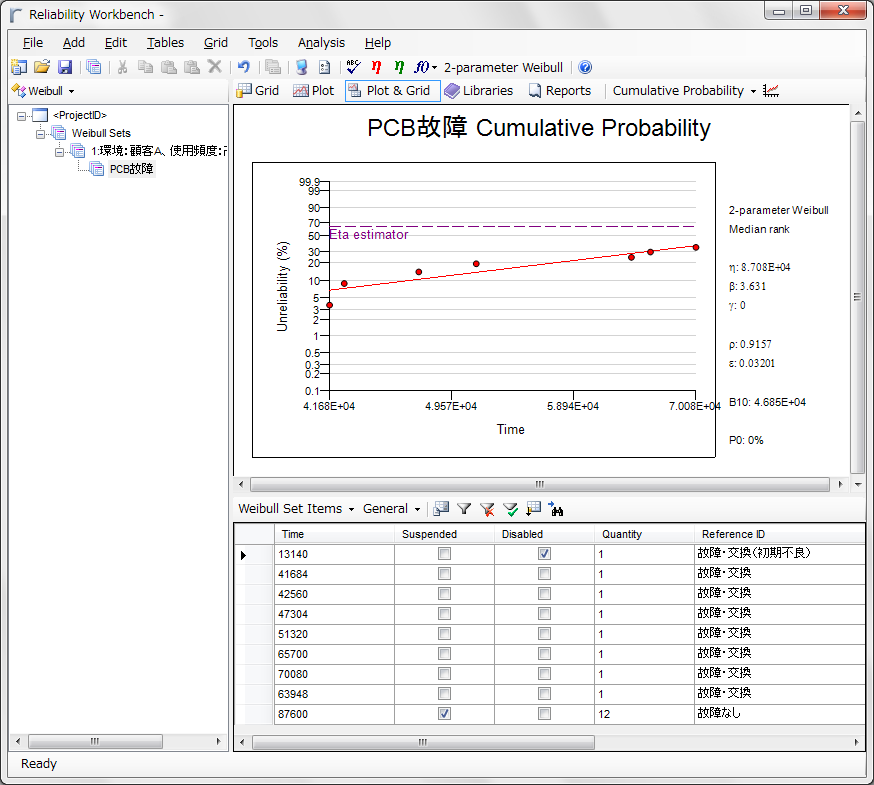
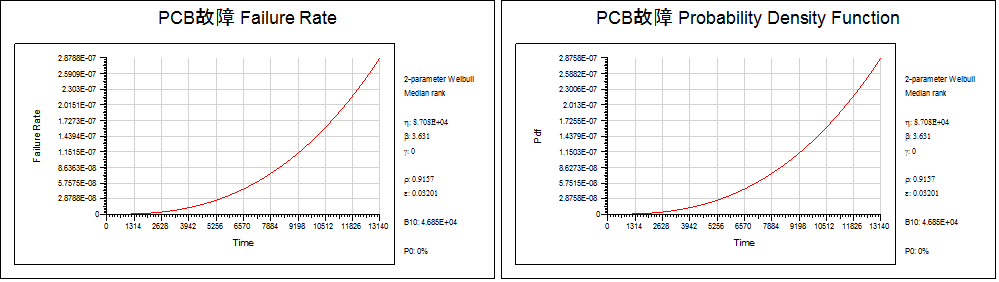
上記ワイブル近似の例では、B10(不信頼度が10%になる時期)が4.685x104であり、このことは、10台中の1台目が故障するのが約5.4年であることを示しています。
数値モデルのまとめ
計算した数値モデル一式を、以下の整理項目を用いて、「故障の数値モデル一覧」として整理します。 整理表の中には、目安として、B-Lifeを含めます。 B-Lifeは、ターゲットとして指定した不信頼度へ達するまでの時間であり、保全や検査周期の目安となります。
- 機種仕様(機種等)、使用環境、使用頻度
- 数値モデルと母数(パラメタ)
- B-Life(不信頼度到達時期)
- 不信頼度や故障率に含まれる故障モード(原因や要因)の分布(パーセンテージ)
- 情報源
信頼性・安全性評価への適用支援
プラントや製品の実際の故障情報に基づいた故障の数値モデルを用いることで、時間に依存する信頼性や安全性の評価を行うことができます。 弊社では、これらの実施支援を行います。
Reliability Workbenchを用いた信頼性評価の例をメルマガ No#10内に示しています。 以下に、RBD(信頼度ブロック図 メルマガNo#10より引用)を用いて、評価の例を示します。
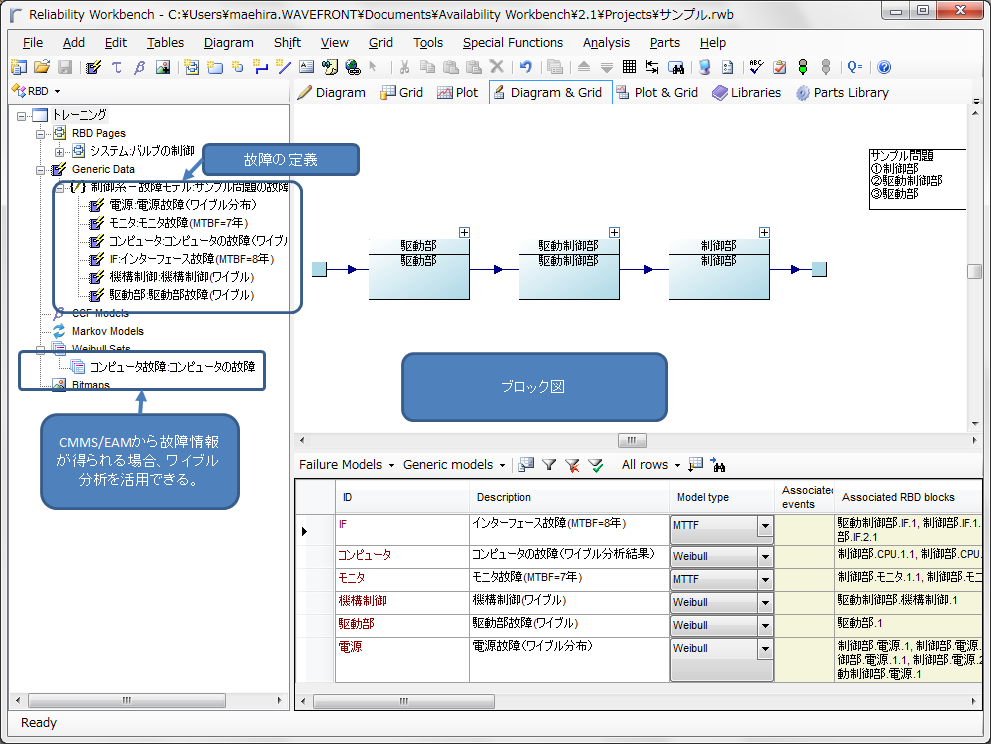
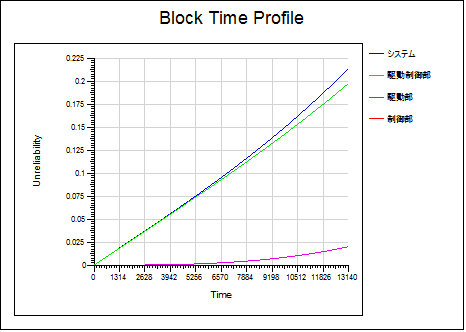
RBD(信頼度ブロック図)分析の例は、こちら(メルマガNo#10の補足資料)をご参照ください。
- 信頼性ブロック図分析(RBD)
信頼度ブロック図を用いることで、システムの信頼性評価、カットセット分析、機器の重要度評価、 感度解析(リスク増加価値、リスク低減価値)を実施できます。
- フォルトツリー分析(FTA)
信頼度ブロック図を用いることで、リスクやハザード確率の評価、カットセット分析、機器の重要度評価、感度解析(リスク増加価値、リスク低減価値)を実施できます。
- イベントツリー分析(ETA)
リスクやハザード発生時、その進展状況とコンシーケンスの頻度を評価することができます。
可用性(稼働率)・LCC推定/評価支援
プラントや製品の実際の故障情報に基づいた故障の数値モデルを用いた上で、 信頼性や安全性評価に故障の原因を排除するための作業(保全作業や検査)を考慮することで、稼働率やLCCの推定及び評価を行うことができます。 推定及び評価は、Availability WorkbenchのRCMCostやAvSim機能を用います。弊社では、これらの実施支援を行います。
Availability Workbenchを用いた稼働率推定の例をメルマガ No#10内に示しています。 以下に稼働率及びリソースの推定の例(メルマガNo#10より引用)を示します。
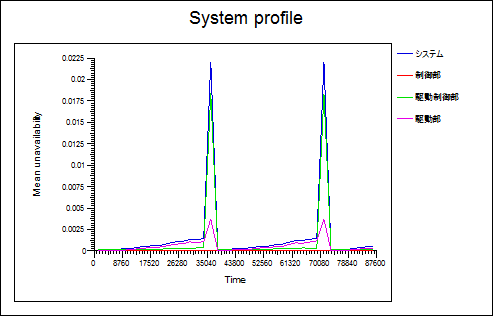
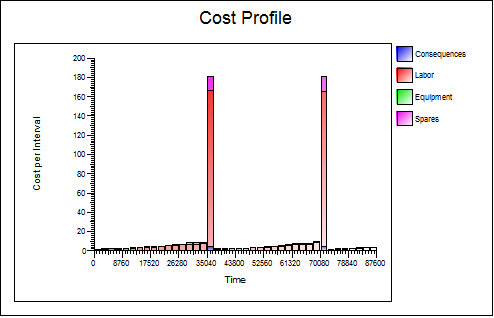
稼働率、必要リソースの推定例は、こちら(メルマガNo#10の補足資料)をご参照ください。
RCMCost機能を利用することで、定期保全、検査の有効性や適正周期を評価することができます。 適正周期は、LCCを最小化する様な周期、稼働率を最大化する様な周期を目標関数とすることが可能です。
AvSimを利用することで、システムを構成するアイテムに不信頼度や故障率を考慮することができます。 これらの構成アイテムに対して適切な保全を実施することで考慮した不信頼度や故障率をリセットすることができます(寿命の延長)。 また、検査の実施は、不信頼度や故障率の成長を監視し、状況に応じて、保全を実施することを意味します。 以上を考慮した上での稼働率、保全、検査の実施、費用を推定することができます。
関連